Our Team’s Journey:
In the exciting world of 3D printing, our three dynamic mechanical engineers found common ground while working at a 3D printing company. However, our enthusiasm was met with a painful truth – 3D printing machines, components, or even materials are all imported from foreign companies. This realization ignited our mission: to grow the 3D printing community by providing the highest quality products made in Vietnam, competitive prices, and optimal customer service for the local 3D printing community.
From finding a single extruder head to purchasing the motor and having all the parts designed and machined, everything in our project is developed from the ground up.
Our main website: http://3dsigmalab.com
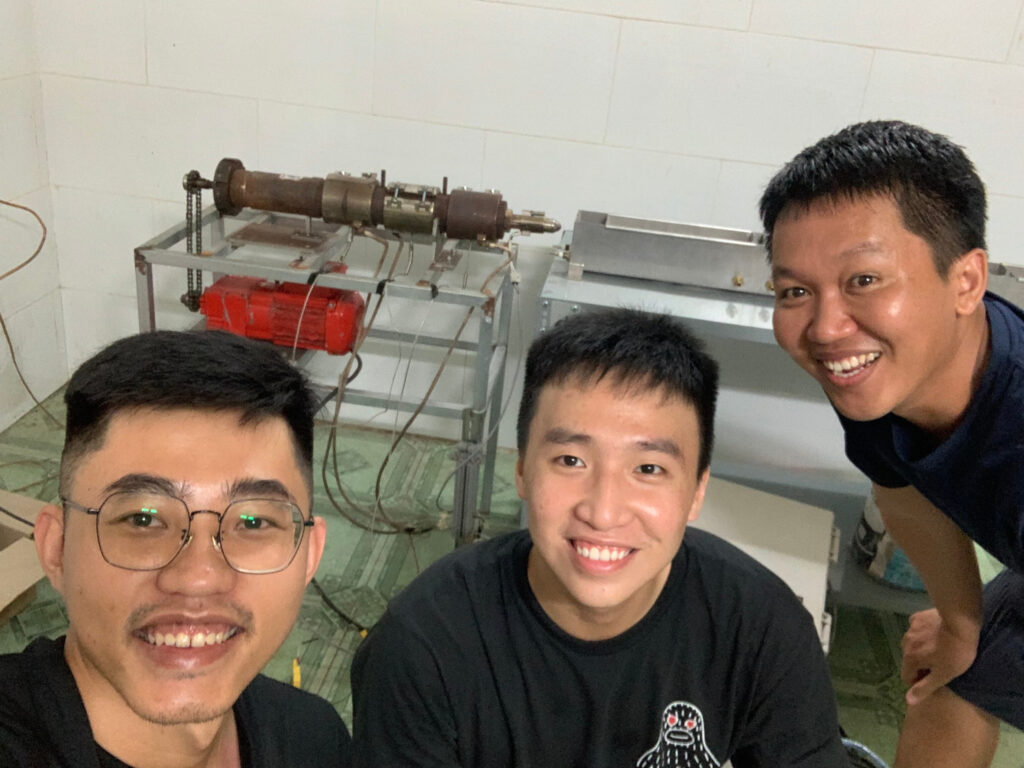
Duy, Nhan & Chi (From Left To Right)
Research and Development Process:
To maintain affordability for our filament project, we opted not to invest in an expensive production line, which can cost over $20,000. Instead, we adopted a DIY (do-it-yourself) approach, constructing everything from the ground up to minimize costs. This reflects our creative spirit and autonomy in product development, enabling us to achieve substantial cost savings compared to using pricey production lines. We take pride in being a team of young engineers in Vietnam who have successfully researched and developed 3D printing filament products from scratch. We possess a clear understanding of the technical factors involved in filament production.
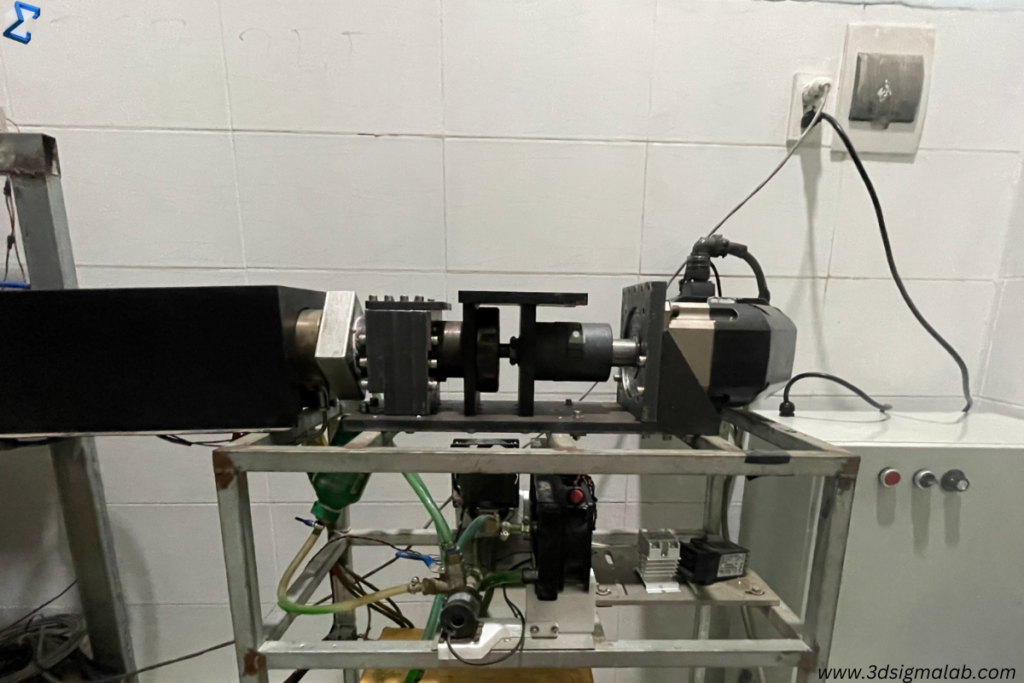
State 1: Find and buy important equipment
We use a plastic injection process with a single-axis extruder. The material is melted, homogenized and then formed into a fibrous shape after exiting the extrusion screw. In this process, the necessary equipment includes a single screw press, DC motor and heating elements. All are purchased and each individual part is tested for functionality before being assembled into a complete line.
Phase 2: 3D CAD Design and Engagement with Processing Service Providers
In addition to the OEM equipment mentioned above, which constitutes the majority of the Extruder assembly, other components in the production process include hot and cold water tanks, pullers, buffers, and winders. It’s important to note that the remaining assembly parts are not included.
As a team of engineers, we navigated through the entire design process, from conceptualization to detailed drawings, collaborating with the manufacturer and assembling everything ourselves. This involved connecting and programming the Arduino to control motors, sensors, heating elements, and more. We possess a comprehensive understanding of every detail of our production line and how to optimize it for 3D printing filament production.
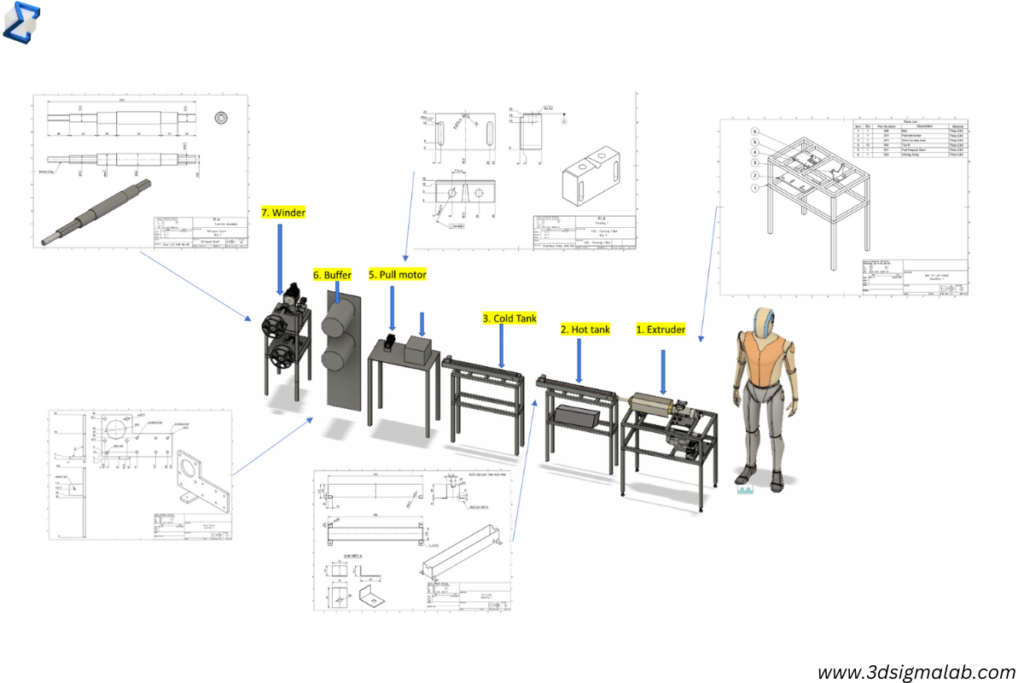
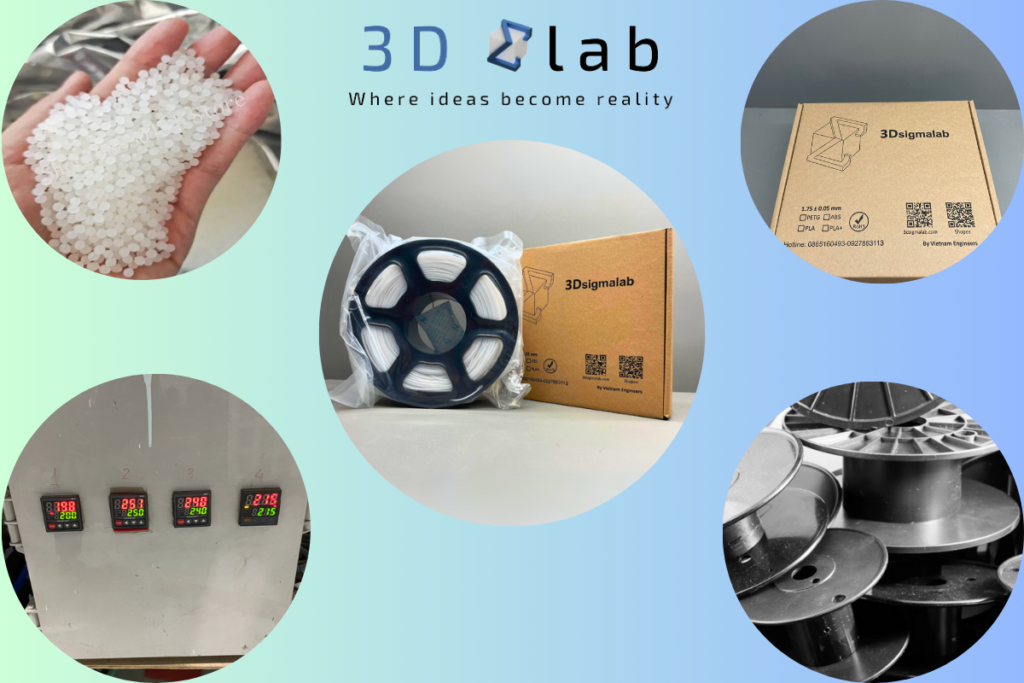
Stage 3: Everything Else – Raw Materials, Testing, Packaging, etc.
This stage is perhaps the longest and most complex, characterized by numerous changes and adjustments. Throughout this process, we faced numerous challenges, including finding the right materials, identifying areas of the production line that required upgrades, and selecting top suppliers for materials, components, and strategic packaging. This phase demands a significant investment of time and effort because every mistake incurs a cost.
The ultimate goal is to create a final product that is not only excellent in quality but also competitive in price and customization.